The 5005 aluminum tube has medium strength, making it suitable for machining and bending. It offers excellent corrosion resistance and weldability, making it ideal for decorative anodizing.
If you require a high-quality anodized surface finish, please specify your anodizing quality requirements when placing your order.
Specifications of 5005 aluminum tube
- B210
- B483
- EN573
- EN755
- EN754
Popular products of 5005 aluminum tube
5005 cold drawn aluminum tube
Cold drawing is a process where aluminum tubes are stretched through a die at low temperatures to achieve the desired dimensions and shapes.
- High Precision: Cold drawn aluminum tubes offer greater dimensional accuracy, suitable for applications with strict size requirements.
- High Surface Finish: The cold drawing process results in a smoother surface, reducing the need for subsequent processing steps.
- Increased Strength: Cold working hardens the material, making the strength of cold drawn aluminum tubes higher than that of untreated raw material.
Mechanical Properties of 5005 Cold Drawn Aluminum Tube:
Temper | Wall thickness (mm) | Tensile Strength (MPa) | Yield Strength (MPa) | Elongation (%) | Hardness (HB) |
O, H111 | ≤ 20 | Min. 100 Max. 140 | Min. 40 | 18 | 30 |
H14 | ≤ 5 | Min. 140 | Min. 110 | 6 | 45 |
H18 | ≤ 5 | Min. 185 | Min. 155 | 4 | 55 |
5005 extruded aluminum tubes
Extrusion is a high-temperature process that involves forcing aluminum billets through a die to create tubular shapes. This process allows for the rapid manufacturing of aluminum tubes in various shapes and has high production efficiency.
- Good Formability: The extrusion process can produce 5005 aluminum tubes in various cross-sectional shapes, suitable for a wide range of sizes and designs.
- High Production Efficiency: The extrusion process enables quick mass production of 5005 aluminum tubes at lower costs.
- Relatively Lower Strength: Compared to cold-drawn tubes, extruded aluminum tubes have relatively lower strength.
Mechanical Properties of 5005 Extruded Aluminum Tubes:
Temper | Wall thickness (mm) | Tensile Strength (MPa) | Yield Strength (MPa) | Elongation (%) | Hardness (HB) |
F, H112 | All | Min. 100 | Min. 40 | 18 | 30 |
O, H111 | ≤ 20 | Min. 100 Max. 150 | Min. 40 | 20 | 30 |
5005 aluminum tube sizes
Mastar offers 5005 aluminum tubes in a wide variety of shapes and sizes. For custom size requirements, please contact us.Quick Quote
- 5005 Aluminum Round Tube
- Diameter: 1-10mm
- Wall Thickness: 0.125mm - 0.75mm
- Length: 1-6 meters (Customizable)
- 5005 Aluminum Rectangular Tube
- Dimensions: 1×2mm to 8×12mm
- Wall Thickness: 0.125mm - 0.5mm
- Length: 1-6 meters (Customizable)
- 5005 Aluminum Rectangular Tube
- Diameter: 1-10mm
- Wall Thickness: 0.125mm - 0.75mm
- Length: 1-6 meters (Customizable)
Beyond 5005 aluminum round, rectangular, and square tubes, Mastar also maintains stock of similar shapes in other alloys — including round, square, and flat tubes in 6061, 5052, 6082, and more. Click the corresponding product type to explore more alloy options, or visit our aluminum tube catalog for a full overview. Feel free to contact our team for tailored solutions.
Chemical elements of 5005 aluminum tube
Chemical Element | % Presen |
Manganese (Mn) | 0.0 - 0.20 |
Iron (Fe) | 0.0 - 0.70 |
Copper (Cu) | 0.0 - 0.20 |
Magnesium (Mg) | 0.50 - 1.10 |
Silicon (Si) | 0.0 - 0.30 |
Zinc (Zn) | 0.0 - 0.25 |
Chromium (Cr) | 0.0 - 0.10 |
Others (each) | 0.0 - 0.05 |
Others (total) | 0.0 - 0.15 |
Aluminum (Al) | Balance |
Physical properties of 5005 aluminum tube
Physical Property | Value |
Density | 2.70 g/cm³ |
Melting Point | 655 °C |
Thermal Expansion | 23.5 x10^-6 /K |
Modulus of Elasticity | 69.5 GPa |
Thermal Conductivity | 201 W/m.K |
Electrical Resistivity | 0.033 x10^-6 Ω .m |
Electrical Resistivity | 52 % IACS |
Equivalent specifications for 5005 aluminum tubes
UNS A95005,ISO AlMg1,BS N41,A-G0.6,EN AW-5005,AMr1
Advantages of 5005 aluminum tubes
- Excellent Corrosion Resistance: Highly resistant to corrosion, even in harsh environments.
- Good Anodizing Performance: Provides a uniform, attractive finish after anodizing.
- Outstanding Weldability: Compatible with various welding methods, with minimal color change post-weld.
- Great Formability: Easy to process, suitable for creating complex shapes.
- Lightweight: Offers moderate strength while being lightweight.
- Eco-Friendly and Recyclable: 100% recyclable, supporting environmental and sustainability goals.
Applications of 5005 aluminum tubes
- Construction Industry: Used as lightweight, corrosion-resistant tubing and support structures in building frameworks.
- Fluid Transport Pipes: Ideal for corrosion-resistant piping in food processing and chemical equipment.
- Radiator Tubes: Widely applied in cooling systems due to its excellent corrosion resistance and thermal conductivity.
- Automotive Tubing: Used in lightweight structural components like fuel lines and cooling system pipes in vehicles.
- Marine Tubing: Serves as lightweight, corrosion-resistant tubing for fluid transport and structural support in ships.
- Tanks and Containers: Suitable for chemical storage tanks and containers.
- Cable and Conduit Pipes: Used in electrical equipment for cable protection and conductor coverings.
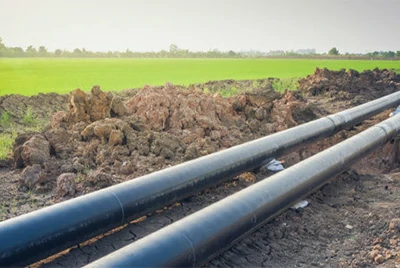
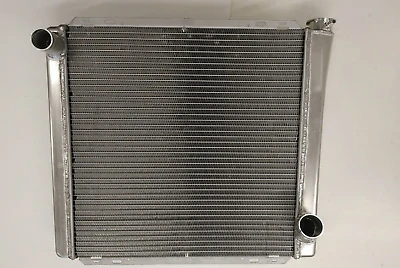
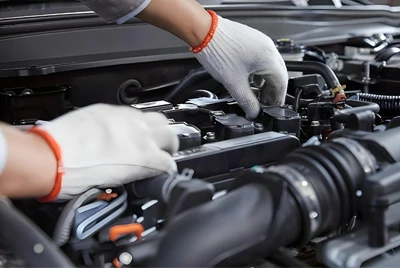
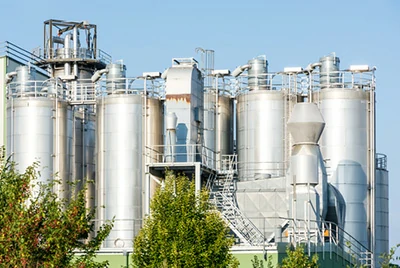
5005 aluminum tubes are ideal for anodizing
- After anodizing, the surface film of 5005 aluminum is clearer and lighter than 3003, matching the color of 6063 architectural extrusions, making it ideal for applications with strict aesthetic requirements.
- Although 5052 is often used as a substitute for 5005, 5052 is more prone to defects and color variations.
- While 5005 and 3003 have similar properties, 5005 delivers better anodizing results with a brighter oxide layer.
- In some cases, anodizing 5005 aluminum tubes may result in streaks.
- It's recommended to test anodizing performance with sample parts before mass production to ensure quality standards are met.
Welding of 5005 aluminum tubes
- Preferred Welding Methods: GMAW (Gas Metal Arc Welding, also known as MIG) and GTAW (Gas Tungsten Arc Welding, also known as TIG) are the primary welding methods.
- Pre-Weld Preparation: 5005 aluminum must be thoroughly clean and dry to prevent contamination and porosity in the weld.
- Filler Metals: Recommended filler metals include 1100, 4043, 4047, or 1188. Among these, 4043 provides the highest crack resistance, 4047 reduces crack sensitivity, and 1188 offers the best color match, particularly for anodized applications.
- Filler metal 1100 is suitable for general welding needs, while a filler alloy similar to 5005 is recommended when matching the base material is critical.
- Heat-Affected Zone (HAZ): Welding 5005 aluminum can reduce material strength in the HAZ.
- Post-Weld Treatments: For thicker or high-stress components, consider annealing or natural aging after welding to relieve internal stresses and improve structural strength.
Processing of 5005 aluminum tubes
- In the soft temper state, the machinability of 5005 is poor, but it improves with increased temper hardness (such as H34 and H38).
- 5005 aluminum is generally not hot worked but can undergo necessary heat treatment in the range of 400 to 700°F.
- The machining accuracy of 5005 aluminum depends on high speed, adequate lubrication, sharp tools, positive rake angles, sufficient clearance, and continuous cutting.
- Sharp tools made from high-speed steel or carbide should be used for machining 5005 aluminum.
- In punching and shearing processes, the clearance between the punch and die for H32 and H34 temper should be 6% of the thickness on each side.
Quality inspection reports – traceable
Our products undergo strict quality control, and we provide a complete set of quality inspection reports.
- Ultrasonic Testing: Ensures no internal defects.
- Chemical Composition Analysis: Complies with industry standards.
- Mechanical Property Testing: Validates product strength.
- Non-Destructive Testing: Comprehensive hazard checks.
- Visual Inspection: Pursuing perfection.
- Anodizing Quality Inspection: Meets industry standards and customer requirements.
- Traceability Records: Fully traceable throughout the process.