An anodized aluminum tube is an aluminum tube that has undergone anodizing treatment, resulting in a durable oxide film on its surface. This process significantly enhances the tube's corrosion resistance and abrasion resistance, while also improving its visual appeal, even in extreme environments.
With its superior oxidation resistance, lightweight, high strength, and excellent wear resistance, anodized aluminum tubes are widely used in industries such as aerospace, automotive manufacturing, construction decoration, and electronic devices. They meet the high standards and diverse requirements across various industries. Whether in performance or appearance, anodized aluminum tubes are indispensable high-performance materials in modern industry.
Click to view the Ultimate Guide to Anodized Aluminum Tubes.
Basic information for anodized aluminum tubes
Alloys: 6005, 6060, 6061, 6063, 6082, 6463, 7075
Temper: T4, T5, T52, T6, T832
Shapes: Round, Square, Rectangular, Oval
Length: Standard 6m, up to 13m
Oxidation Grade: Type I, Type II, Type III
Oxide Thickness: Standard oxidation thickness 5-25μm, hard anodizing thickness 25-100μm
Colors: Clear, Silver, White, Black, Light Bronze, Medium Bronze, Dark Bronze, Extra Dark Bronze, Gold, Light Champagne, Red, Blue, Purple, Green
Surface Finishes: Etched, Clear, Sandblasted, Brushed, Polished, Mirror
Post-Processing: Cutting, Drilling, Tapping, Milling, CNC machining, Bending
Minimum Order Quantity (MOQ): Accepts small orders, with a minimum order of 500kg
Production Time: 25 to 40 days, depending on order complexity and specifications
Packaging: Pearl membrane wrap, Wooden boxes/wooden pallets
What types of anodized aluminum tubes does Mastar offer?
- Anodized Aluminum Round Tubing
- Alloys: 6061, 6063, 6060, 6082, 6005, 2024, 7075
- OD: 0.4" - 16" (10-420mm)
- Anodized aluminum round tubing is widely used in structural support and fluid conveyance systems due to its uniform strength and lightweight properties. Its smooth surface not only enhances corrosion resistance, but also improves its performance in aerospace and automotive applications.
- Anodized Aluminum Square Tubing
- Alloys: 6061, 6063, 6060
- size: 0.2" - 8" (5-200mm)
- Anodized aluminum square tubing provides excellent strength and rigidity, making it ideal for architectural decoration and frame structures. Its unique appearance and abrasion resistance make it widely used in modern homes and commercial spaces.
- Anodized Aluminum Oval Tubing
- Alloys: 6061, 6063, 6060, 2024
- Size: 0.4" - 16" (10-420mm)
- The streamlined design of anodized aluminum oval tubing makes it particularly popular in the automotive and bicycle industries, as it reduces aerodynamic drag while enhancing its aesthetics. Its excellent oxidation resistance ensures long-term use in various environments.
- Anodized Aluminum Rectangular Tubing
- Alloys: 6061, 6063, 6060
- Size: 0.2" - 8" (5-200mm)
- Anodized aluminum rectangular tubing offers excellent load-bearing capacity and adaptability, making it widely used in mechanical structures and furniture manufacturing. Its durable anodized aluminum film enhances abrasion resistance and corrosion resistance, ensuring excellent performance across various applications.
What Other Types of Anodized Products Can Mastar Provide?
- Seamless Aluminum Tubing
- Cold Drawn Aluminum Tubing
- Thin Wall Aluminum Tubing
- Thick Wall Aluminum Tubing
- Telescopic Aluminum Tubing
- Threaded Aluminum Tubing
- Aluminum Cylinder Tubes
- Aluminum streamlined Tubes
- Custom Aluminum Tubing
What are the popular alloys for Mastar's anodized aluminum tubes?
- 6061 T6 Anodized Aluminum Tube
- Standard: EN 755, ASTM B221, ASTM B241
- Application: Aerospace, Automotive
- 6063 T5/T52 Anodized Aluminum Tube
- Standard: EN 755, ASTM B221, ASTM B241
- Application: architectural decoration, guardrail, furniture
- 6060 T5/T6 Anodized Aluminum Tube
- Standard: EN 755, ASTM B221
- Application: Construction, Electrical Conduit, Furniture Upholstery
- 6005 T5 Anodized Aluminum Tube
- Standard: EN 755, ASTM B221
- Application: rail transit, building bridges
- 6082 T6 Anodized Aluminum Tube
- Standard: EN 755, ASTM B221
- Application: Structural Frame, Aerospace
- 6066 T4/t6 Anodized Aluminum Tube
- Standard: EN 755, ASTM B221
- Application: high-end bicycles, aerospace
- 5052 O Anodized Aluminum Tube
- Standard: EN 755, ASTM B221
- Application: Fuel Line, Hydraulic Line
- 5083 H112 Anodized Aluminum Tube
- Standard: EN 755, ASTM B221, ASTM B241
- Application: marine ships, petrochemicals
- 5086 H111 Anodized Aluminum Tube
- Standard: EN 755, ASTM B221, ASTM B241
- Application: Marine Industry, Low Temperature Field
- 7003 O Anodized Aluminum Tube
- Standard: EN 755, ASTM B221
- Application: automotive manufacturing, aerospace
- 7005 T5/T6 Anodized Aluminum Tube
- Standard: EN 755, ASTM B221
- Application: Bicycle Frame, Outdoor Sports Equipment
- 7075 T6 Anodized Aluminum Tube
- Standard: EN 755, ASTM B221, ASTM B241
- Application: aerospace, oil drill
What colors are available for Mastar anodized aluminum tubes?
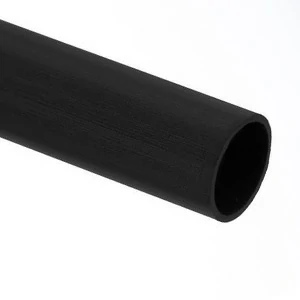
Black Anodized Aluminum Tube
Black anodized aluminum tube is a popular choice in architectural design due to its modern appearance. The 20μm thick anodized layer effectively absorbs dye and provides excellent abrasion resistance, making it ideal for window frames, partition walls, and other applications where durability and aesthetics are important.
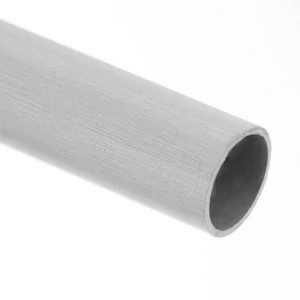
Clear (Silver) Anodized Aluminum Tube
Clear anodized aluminum tube (also known as silver anodized aluminum) is known for its low maintenance and bright appearance, making it suitable for a variety of design environments. Its sleek silver finish combines aesthetics and functionality, making it perfect for architectural structures and design elements. This anodized finish requires no special treatment and maintains its perfect appearance for a long time.
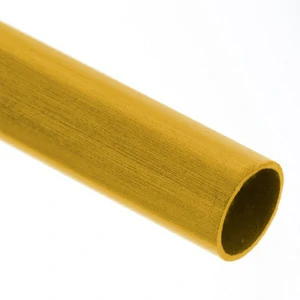
Gold Anodized Aluminum Tube
Gold anodized aluminum tube adds a luxurious touch to any project with its bright gold surface, making it suitable for various size requirements and offering a unique style. Combining durability and elegance, this material is perfect for high-end design solutions.
Mastar's Anodized Aluminum Tubes Offer Various Color Options, Including:
- Clear Satin anodized aluminum tube
- Champagne anodized aluminum tube
- Bronze anodized aluminum tube
- Red anodized aluminum tube
- Blue anodized aluminum tube
- Lilac anodized aluminum tube
Best applications for anodized aluminum tubes
Architectural decoration
Anodized aluminum tubes play a vital role in architectural decoration, commonly used for door and window fittings, handrails, and partitions. Their high corrosion resistance and elegant appearance make them indispensable in modern architectural design. Additionally, anodizing enhances the decorative effect of the surface, making them suitable for railings, curtain rods, clothes rods, bathroom shelves, wardrobe tracks, and other home accessories.
Outdoor sporting equipment
In outdoor sporting equipment, anodized aluminum tubes are favored for their lightweight and durability. Their corrosion resistance and excellent mechanical properties make them ideal for applications in bicycle frames, tent poles, hiking sticks, golf clubs, skiing equipment, and other sporting goods. These tubes ensure the stability and safety of equipment in various environments.
Medical equipment
Medical equipment requires materials with hygiene and durability standards, and anodized aluminum tubes are the perfect choice. With their smooth, scratch-resistant surface, anodized tubes help maintain the cleanliness of medical equipment, reducing contamination risks. They are widely used in surgical instruments, probe holders, medical tools, and monitoring devices.
Optical components
Anodized aluminum tubes also find important applications in optical components. The anodized surface can be dyed in various colors and has a low reflectivity, making it ideal for use in optical instrument housings, camera lens tubes, optical instrument accessories, and other related products. This significantly enhances the durability of optical equipment.
Automotive manufacturing
In the automotive manufacturing industry, anodized aluminum tubes are extensively used for vehicle body structures, fuel conduits, and interior parts due to their lightweight and high strength. The anodizing process provides additional protection and aesthetic benefits, enhancing both the appearance and durability of vehicles, meeting the design requirements of modern cars.
Pneumatic systems
Anodized aluminum tubes excel in pneumatic systems, where they must withstand high pressure and provide excellent abrasion resistance. These tubes are an essential component in pneumatic equipment, valves, cylinder tubes, and compressors, ensuring efficient operation of these systems.
Why choose Mastar's anodized aluminum tubes?
Mastar is a manufacturer focused on high-quality aluminum products, dedicated to providing exceptional products and services to customers. Our professional team, composed of experienced technical experts, is capable of meeting the diverse needs of various industries.
By choosing Mastar as your anodized aluminum tube supplier, you will enjoy the following advantages:
- High Quality Standards: We follow strict manufacturing processes to ensure every anodized aluminum tube meets international standards, providing outstanding corrosion resistance and abrasion resistance.
- Extra Long Products: We offer anodized aluminum tubes up to 13 meters in length to meet the needs of various complex applications.
- Custom Solutions: We can customize anodized aluminum tubes according to your specific requirements, including black anodizing for unique aesthetic effects and durability.
- Rich Experience: With years of industry experience, we have accumulated unique expertise in solving complex technical challenges.
- Flexible Production Capability: Whether for small batch or large-scale production, we can quickly respond to your needs and ensure fast delivery.
- Comprehensive After-Sales Support: Our service team is always by your side, providing comprehensive after-sales support to ensure you have no concerns during use.
Ultimate guide to anodized aluminum tubes
Here is all the essential knowledge about anodized aluminum tubes. If you have any questions, you can find the answers here.
You will learn everything about production processes, specifications, workability, quality requirements, and more.
Table of Contents
- What are anodized aluminum tubes?
- What types of anodizing processes are available?
- What is the specific process flow for anodizing?
- What are the significant advantages of anodized aluminum tubes?
- What is black anodizing?
- What are the benefits of black anodizing?
- Can all aluminum alloys be anodized?
- What is the typical lifespan of anodized aluminum tubes?
- Can anodized aluminum tubes be used directly for aesthetic purposes?
- Can anodized aluminum tubes be bent?
- Can anodized aluminum tubes be welded?
- Can anodized aluminum tubes be machined?
- What is the difference between regular anodizing and hard anodizing?
- How to conduct quality testing on anodized aluminum tubes?
What are anodized aluminum tubes?
Anodized aluminum tubes are aluminum tubes treated with the anodizing process, forming a hard, corrosion-resistant oxide layer on their surface. This process creates an oxidized layer on the aluminum tube through an electrolytic reaction, significantly enhancing abrasion resistance and corrosion resistance, while also improving the aesthetic appearance.
What types of anodizing processes are available?
Type I Anodizing
Oxide film thickness: ≤5μm
Also known as passivation, this process typically involves treatment with chromic acid or manganese acid solutions, forming a thin oxide layer (not exceeding 5 microns) on the aluminum alloy surface. Although thin, the resulting oxide layer offers excellent corrosion resistance and good adhesion. This process is commonly used when products require continuous electrical conductivity.
Type II Anodizing
Oxide film thickness: 5-20μm
This process is carried out using sulfuric acid electrolyte for electrochemical oxidation, and the resulting oxide film thickness typically ranges from 5 to 20 microns, sometimes exceeding 25 microns. The porous oxide layer provides superior corrosion resistance and dyeing capabilities, making it suitable for applications in construction, transportation, and home appliances where aluminum products require painting.
Type III Anodizing
Oxide film thickness: 25-100μm
Also known as hard anodizing, this process is conducted at lower temperatures and higher voltages, creating an oxide film with a thickness of 25-150 microns. This layer is significantly harder than the standard sulfuric anodizing film, with a hardness exceeding 300 HB, offering superior abrasion resistance and heat resistance. This type is primarily used in automotive, aerospace, and heavy industrial components, particularly for high wear and impact applications.
Type IV Anodizing (Micro-Arc Oxidation)
Micro-arc oxidation (MAO), also known as microplasma oxidation (MPO), forms a ceramic-like oxide film at higher voltages, reaching a hardness of over 1000 HB, comparable to hard steel. This process is used for components requiring extremely high abrasion resistance, such as pistons, bearings, and connectors.
What is the specific process flow for anodizing aluminum tubes?
Pre-Anodizing treatment
De-oiling and cleaning
First, the aluminum tubes must be cleaned to remove any oils generated during the extrusion or drawing process. A suitable degreaser, such as an alkaline cleaner (e.g., sodium hydroxide solution) or solvents (e.g., acetone or isopropanol), should be used.
The degreaser is applied evenly or the aluminum tube is immersed to ensure thorough coverage. For large diameter tubes, consider using spraying or immersion cleaning.
Afterward, rinse the aluminum tube thoroughly with pure water to remove any remaining degreaser and dissolved contaminants, ensuring an even flow of water over each tube surface.
The cleanliness of the aluminum tube is crucial for the adhesion and uniformity of the anodized layer, so this step must be handled carefully.
Alkaline etching (pickling)
Etching, also known as alkaline cleaning, requires the use of a suitable etching solution. Typically, sodium hydroxide (caustic soda) or an acidic etchant (such as diluted sulfuric acid) is used. The selection depends on the specific aluminum alloy and desired effects.
The aluminum tube is immersed in the etching solution, ensuring that all surfaces are evenly exposed. The etching process usually lasts from several minutes to about ten minutes.
After the etching, rinse the tube immediately with pure water to remove any etching solution and by-products from the reaction.
Alkaline etching effectively removes the natural oxide film from the surface and increases surface roughness, which improves the adhesion of the subsequent anodizing layer.
Neutralization and rinsing
After alkaline etching, neutralize the tube by immersing it in dilute nitric acid, which helps remove any remaining fine particles and residues from the etching process.
Once the neutralization is complete, thoroughly rinse the aluminum tube with pure water to ensure that all chemical residues are removed.
Ensuring the surface is free of any impurities before anodizing will enhance the quality of the anodizing process.
Chemical polishing
Chemical polishing is a key step where aluminum tubes are immersed in a strong acid solution, usually a combination of sulfuric and phosphoric acids or a three-acid mixture (sulfuric, phosphoric, and nitric acid).
The aluminum reacts with the acidic solution, removing surface impurities and resulting in a smoother, more polished appearance. This step significantly enhances the surface finish, which is important for the subsequent anodizing treatment.
After chemical polishing, rinse the aluminum tube with pure water to remove any acid residues and use a neutralizing solution to neutralize the remaining acidity. Finally, perform three consecutive water rinses to ensure the tube is thoroughly clean, laying the foundation for effective anodizing.
Setting up the anodizing bath
Bath construction
When constructing the anodizing bath, use suitable materials like polypropylene or PVC, as they provide excellent corrosion resistance and electrical insulation.
The bath should be designed with enough space to hold the aluminum tubes and electrolyte solution, while leaving room for the cooling system and electrodes. This ensures the anodizing process can proceed smoothly.
Electrode setup
The cathodes are usually made from lead or graphite, chosen for their corrosion resistance and electrical conductivity. The cathode surface should be kept clean and well-connected to the power source.
The aluminum workpieces to be anodized are mounted on the anode racks, ensuring a stable electrical connection with the anode rods to ensure an effective electrolysis process.
Electrolyte preparation
The electrolyte is typically a 10%-20% sulfuric acid solution, with the concentration adjusted based on the specific requirements of the workpieces. The solution should be mixed evenly to prevent any localized variations in concentration, which ensures a stable and effective electrolytic process.
Temperature control
The optimal temperature range for anodizing is generally between 20°C to 22°C. To maintain this temperature, cooling systems such as cooling coils or heat exchangers are used, and the temperature should be monitored regularly.
If the temperature is too high, the oxide layer may become too porous, affecting its strength and corrosion resistance. If the temperature is too low, the reaction rate may slow down, which can affect the uniformity of the anodizing layer. Thus, temperature control is crucial for achieving optimal anodizing results.
Stirring system
Air stirring, mechanical stirring, or pumping circulation can be used to maintain the uniformity of the electrolyte. Stirring frequency should be regularly monitored and adjusted to avoid localized overheating or sedimentation, which will help ensure the electrolyte remains homogeneous and improve the anodizing effect.
Below is a simple diagram of a typical anodizing tank setup:
+-----------------+ | DC Power Supply| +--------+--------+ | +------+------+ | | | |+--------+-------------+--------+| | | || | Anodizing | || | Tank | || | | || +-------------+ || | | || | Electrolyte| || | Solution | || | | |+--------+-------------+--------+ | | | Cooling | | System | +-------------+
Technical specifications of a typical sulfuric acid anodizing tank:
Electrolyte composition | 10% to 20% sulfuric acid by weight |
Temperature range | 68°F - 72°F(20°C - 22°C) |
Current density | 10 to 20 amperes per square foot (ASF) or 1.1 to 2.2 amperes per square decimeter (ASD) |
Agitation | Air agitation, mechanical stirring, or pumped circulation |
Cathode material | Lead or graphite |
Anode material | Aluminum workpieces to be anodized |
Anodizing process
Submersion in electrolyte
The aluminum tube is slowly immersed into the pre-prepared electrolyte solution, ensuring that it is fully submerged and that no air bubbles form on the surface.
Current activation
The current is activated by connecting a DC power source to the anode and cathode, ensuring a smooth flow of current. The current density is adjusted according to the specific requirements of the finished product, typically kept between 10-20 amps per square foot (ASF). This ensures the effectiveness and uniformity of the anodizing process.
Parameter monitoring
Monitoring the key parameters is crucial for the anodizing process. As the voltage increases, the thickness of the anodized layer also increases. Engineers need to adjust the voltage according to the desired thickness.
The growth rate of the anodized layer should be monitored and recorded. Typically, the growth rate remains between 0.1-1.0 μm/min, which ensures the uniformity and functionality of the anodized layer.
Formation of oxide layer
The anodized layer consists of a barrier layer and a porous layer. The barrier layer provides excellent corrosion resistance, while the porous layer is suitable for subsequent dyeing or sealing treatments.
It is important to maintain stable parameters such as electrolyte composition, temperature, and stirring during the anodizing process, as these factors significantly affect the density and porosity of the oxide layer.
Key parameters and their impact on anodizing process:
Voltage | Determines the thickness of the oxide layer |
Current Density | Influences the growth rate and porosity of the oxide layer |
Anodizing Time | Affects the thickness of the oxide layer |
Electrolyte Composition | Determines the type and properties of the oxide layer |
Temperature | Affects the density, hardness, and porosity of the oxide layer |
Agitation | Influences the uniformity and morphology of the oxide layer |
Post-Anodizing water rinse
After anodizing, rinse the aluminum tube thoroughly with pure water to prevent the oxide layer from being damaged by any residual elements or contaminants.
Following the water rinse, perform an ultrasonic cleaning process to remove any remaining acidic solution, ensuring a clean, contaminant-free surface.
The tube is then subjected to a final round of water rinsing, making sure no residues remain before moving on to the next step, such as coloring treatment.
Coloring treatment
Several methods are used to add color to anodized aluminum:
1.Dyeing: The aluminum tube is immersed in a dye solution to allow the dye to penetrate the oxide layer, creating a permanent color.
2.Electrolytic Coloring: Metal salts are used, and a current is applied to deposit metal ions, forming different colors.
3.Integral Coloring: Dyes are added during the anodizing process, mixing them with the solution to produce more consistent coloring.
Each of these methods can significantly enhance the aesthetic appeal and corrosion resistance of the aluminum tube. The specific choice of method depends on the customer's requirements.
Post-Anodizing treatment
Sealing
Sealing the oxide layer pores improves corrosion resistance and durability.
When sealing, a variety of methods can be used to enhance the performance of the aluminum oxide layer.
First, the aluminum tube is immersed in deionized water at 90-100°C for 15-30 minutes to convert the aluminum oxide into a hydrated form.
Second, a nickel acetate solution can be used for sealing to further improve corrosion resistance.
Chemical cold sealing technology can also be used to retain the original appearance while providing good protection.
Through these sealing treatments, the pores of the oxide layer can be effectively sealed, thereby improving corrosion resistance and durability.
Drying treatment
After sealing and cleaning, the aluminum tube is preheated in a hot water bath to ensure even temperature distribution. It is then moved to a drying oven to completely remove residual moisture, ensuring the tube's surface is dry and free from water spots. This concludes the anodizing process.
What are the significant advantages of anodized aluminum tubes?
- Superior Corrosion Resistance: The anodizing process creates a durable oxide film on the surface of the aluminum tube, significantly enhancing its corrosion resistance. The oxide film effectively resists environmental factors and chemical agents, extending the lifespan of the aluminum tube, especially in harsh conditions.
- Increased Surface Hardness: The oxide film formed during the anodizing process greatly enhances the surface hardness of the aluminum tube, making it more wear-resistant than untreated aluminum. This increased hardness allows anodized aluminum tubes to perform excellently under mechanical friction and impact.
- Scratch Resistance: The surface of anodized aluminum tubes is smooth and hard, making them less prone to scratches. This scratch resistance ensures that the tubes maintain their appearance and performance during transportation and usage.
- Colorability: After anodizing, the surface of the aluminum tube can be easily dyed to meet aesthetic and customization needs. This coloring not only enhances the appearance but also further improves the corrosion resistance of the material.
- Adaptability to Harsh Environments: The wear resistance of anodized aluminum tubes makes them suitable for high-wear environments, such as mining, machinery manufacturing, and oil drilling. The tubes are frequently exposed to abrasives like dust and particles, yet the anodized layer provides effective protection against these impacts.
- Extended Service Life: Due to their excellent abrasion resistance, anodized aluminum tubes have a significantly extended service life, reducing the need for frequent replacements or maintenance, thereby lowering overall operational costs.
What is black anodizing?
Black anodizing is an electrochemical treatment process for aluminum parts. It starts with a standard anodizing process to form a semi-porous oxide layer, which is then dyed black using appropriate dyes.
This process differs from the black oxide coatings that are not suitable for aluminum parts. Black anodized aluminum not only has the advantages of regular anodizing but also provides enhanced abrasion resistance, corrosion resistance, light absorption, and heat dissipation capabilities.
What are the benefits of black anodizing?
Compared to regular anodizing, the main advantages of black anodizing include:
- Enhanced Abrasion and Corrosion Resistance: Black anodizing improves the surface wear resistance of aluminum parts while preventing rust, ensuring their durability in harsh environments.
- Increased Thermal Emissivity: The black dye enhances the aluminum's thermal emissivity, making it suitable for applications like radiators and satellite components, where effective heat dissipation is essential.
- No Outgassing: Properly sealed black anodized parts will not outgas in a vacuum, which is critical for protecting sensitive equipment.
- Excellent Color Fastness: Parts dyed with inorganic salts or metal salts for black anodizing retain their color stability under UV exposure, preventing fading.
Can all aluminum alloys be anodized?
Most aluminum alloys can undergo the anodizing process, including those from the 1000, 3000, 5000, 6000, and 7000 series. However, alloys with high copper or silicon content, such as the 2000 and 4000 series, may require special conditions.
Alloys like 6061, 6063, 6082, 5052, 5083, and 7075 are ideal for anodizing. When selecting specific anodizing processes and setting parameters for the anodizing process, it's important to consider the alloy composition, as this is critical for the outcome.
What is the typical service life of anodized aluminum tubes?
The service life of anodized aluminum tubes is influenced by various factors. If used in marine, chemical, or other corrosive environments, the service life may be slightly reduced. Pressure or high-load applications can also accelerate fatigue damage, shortening the tube's lifespan.
Generally, anodized aluminum tubes can last 15-20 years, and with regular maintenance and inspection, their service life can be significantly extended.
Can anodized aluminum tubes be used directly for appearance parts?
Yes, anodized aluminum tubes are ideal for use in appearance parts due to their excellent surface finish and corrosion resistance.
Through anodizing and coloring processes, a wide variety of colors and finishes can be achieved, enhancing the visual appeal.
Common applications include automotive exterior parts, architectural decorations (such as railings, curtain rods, and wardrobe rods), furniture accessories, medical device components, and electronic product components.
For appearance parts, the thickness of the anodized layer and surface quality must be controlled to ensure the integrity of the anodized coating, guaranteeing long-term performance in harsh environments.
Can anodized aluminum tubes be bent?
While it is generally not recommended to bend anodized aluminum tubes because this may cause the oxide film to crack (especially with high-strength alloys like 6061, 6082, and 7075), it is possible with proper technique.
To minimize the risk of cracking, optimize the bend radius and angle and use alloys with good ductility and toughness to improve the bending performance.
When bending, apply force slowly and evenly to avoid stress concentration and reduce the risk of cracking.
After bending, the tubes can be re-anodized to repair and enhance the oxide layer, improving the surface protection.
You can also contact our engineers to help you quickly understand the specific situation of alumina tube bending.Quick Quote
Can anodized aluminum tubes be welded?
Welding anodized aluminum tubes is relatively complex, but it is possible.
Before welding, the oxide layer must be removed to ensure good adhesion at the weld joint. This can be done through mechanical grinding or chemical cleaning.
TIG welding and MIG welding are commonly used, with TIG being preferred for thinner tubes due to its higher welding quality, while MIG welding is suitable for thicker tubes.
During welding, control the appropriate welding current, speed, and gas shielding to avoid defects like porosity and cracks. After welding, treat the welded area by re-anodizing to restore the oxide layer and maintain its integrity.
Click to learn more about aluminum tube pipe welding.
Can anodized aluminum tubes be machined?
Yes, anodized aluminum tubes can be machined, such as through cutting, drilling, and milling.
However, since the oxide layer is hard, it may cause increased tool wear, requiring adjustments to the machining parameters. Also, machining will remove the anodized layer, exposing the untreated aluminum substrate.
It is generally recommended to machine the aluminum tube before anodizing to avoid damaging the protective oxide layer and reduce the surface protection.
What is the difference between regular anodizing and hard anodizing?
Regular anodizing (also known as Type II anodizing) creates a thinner oxide film (5-25 μm), mainly for decorative and aesthetic purposes. It offers various colors and finishes, typically used for appearance parts.
Hard anodizing (also known as Type III anodizing) creates a thicker oxide film (25-100 μm), known for its high abrasion resistance and corrosion resistance. Hard anodizing requires higher voltage, lower temperature, and longer processing times, resulting in a matte appearance. Colors typically include transparent, gray, or black.
Hard anodizing is often used in aerospace, automotive, and heavy industry applications, especially where high wear and impact resistance are required.
How is the quality of anodized aluminum tubes tested?
The quality of anodized aluminum tubes is tested according to ASTM B244 standards, which include a series of testing procedures specifically designed to evaluate the quality and performance of the anodized coating. This ensures the aluminum tube meets industry standards for thickness, corrosion resistance, and color consistency.
1.Thickness Measurement
The thickness of the anodized layer directly affects its protective performance and durability. Eddy current testing is commonly used to measure thickness according to ASTM B244, where a probe is used to take precise measurements on the tube surface with multiple points tested for reliability.
2.Corrosion Resistance Test
The corrosion performance of the anodized layer is evaluated using salt spray testing (ASTM B117). Samples are placed in a salt spray chamber to simulate a corrosive environment, and corrosion area and type are recorded.
3.Color Consistency Evaluation
Maintaining consistent color is crucial for product aesthetics. A spectrophotometer is used to measure sample values and compare them to standardized color samples (CIELAB standards) to ensure consistency across different production batches.
By analyzing thickness, corrosion, and color data, issues in the process can be identified. Based on the test results, production parameters can be adjusted, and quality control processes updated to ensure the anodized aluminum tubes consistently meet industry standards.